17-4PH Material Data Sheet
Scopes
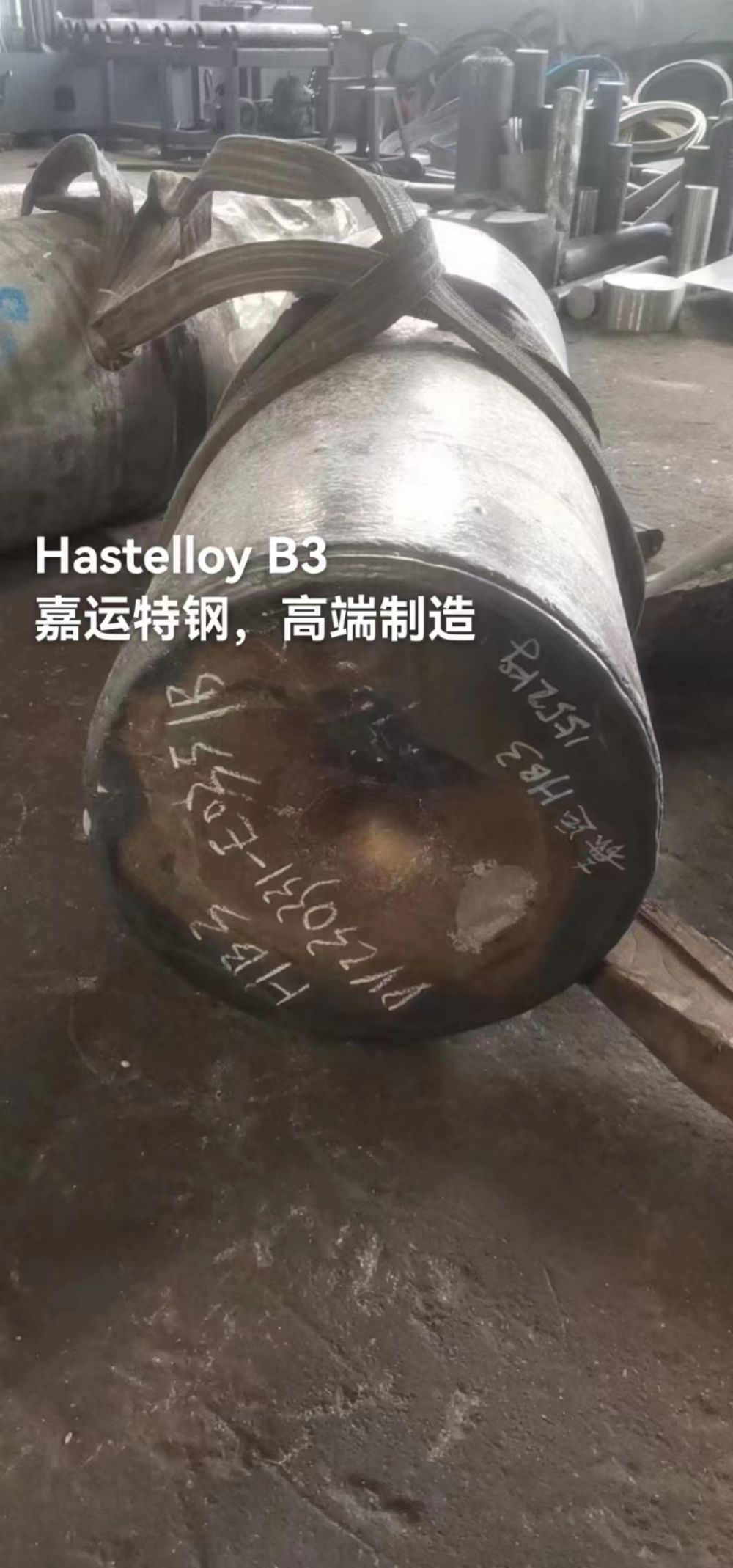
The stainless material 17-4 PH is characterized by a high yield strength, good corrosion resistance and high wear resistance. 17-4 PH is one of the most important steels that can be hardened. It is analytically the same with the materials 1.4548 and 1.4542.
The use in low-temperature range is possible with Condition H1150 and H1025. An excellent notched impact strength is also given at minus temperatures.
Due to the good mechanical properties and corrosion resistance, the material is suitable for use in marine environments, but is susceptible to crevice corrosion in standing seawater.
17-4PH is popularly known as AISI 630.
The material 17-4PH is used in the chemical industry, the wood industry, the offshore sector, in shipbuilding, in mechanical engineering, in the oil industry, in the paper industry, in the sports industry. Leisure industry and as a re-melted version (ESU) in the air and Aerospace.
If mechanical properties and corrosion resistance of martensitic steels are insufficient, 17-4PH can be used.
17-4PH Material Data Sheet Download
Characteristics
Malleable | good |
Weldability | good |
Mechanical properties | excellent |
Corrosion resistance | good |
Machinability | bad to medium |
Advantage
One special property of the material 17-4 PH is the suitability for low temperatures and the applicability up to approx. 315°C.
Forging: The forging of the material takes place in a temperature range of 1180 ° C to 950 ° C. To ensure grain refining, the cooling to room temperature is done with air.
Welding: Before the material 17-4 PH can be welded, consideration must be given to the condition of the base material. In stable form, copper is present in the material. This promotes no hot cracking.
To be able to do the welding optimum welding conditions are required. Undercuts or welding defects can lead to the formation of a notch. That should be avoided. To prevent the formation of stress cracks, the material must be subject again to solution annealing with subsequent aging within a very short time after welding.
If no after-heat treatment takes place, the mechanical-technological values in the weld seam and the heat-affected zone to the base material can be very different.
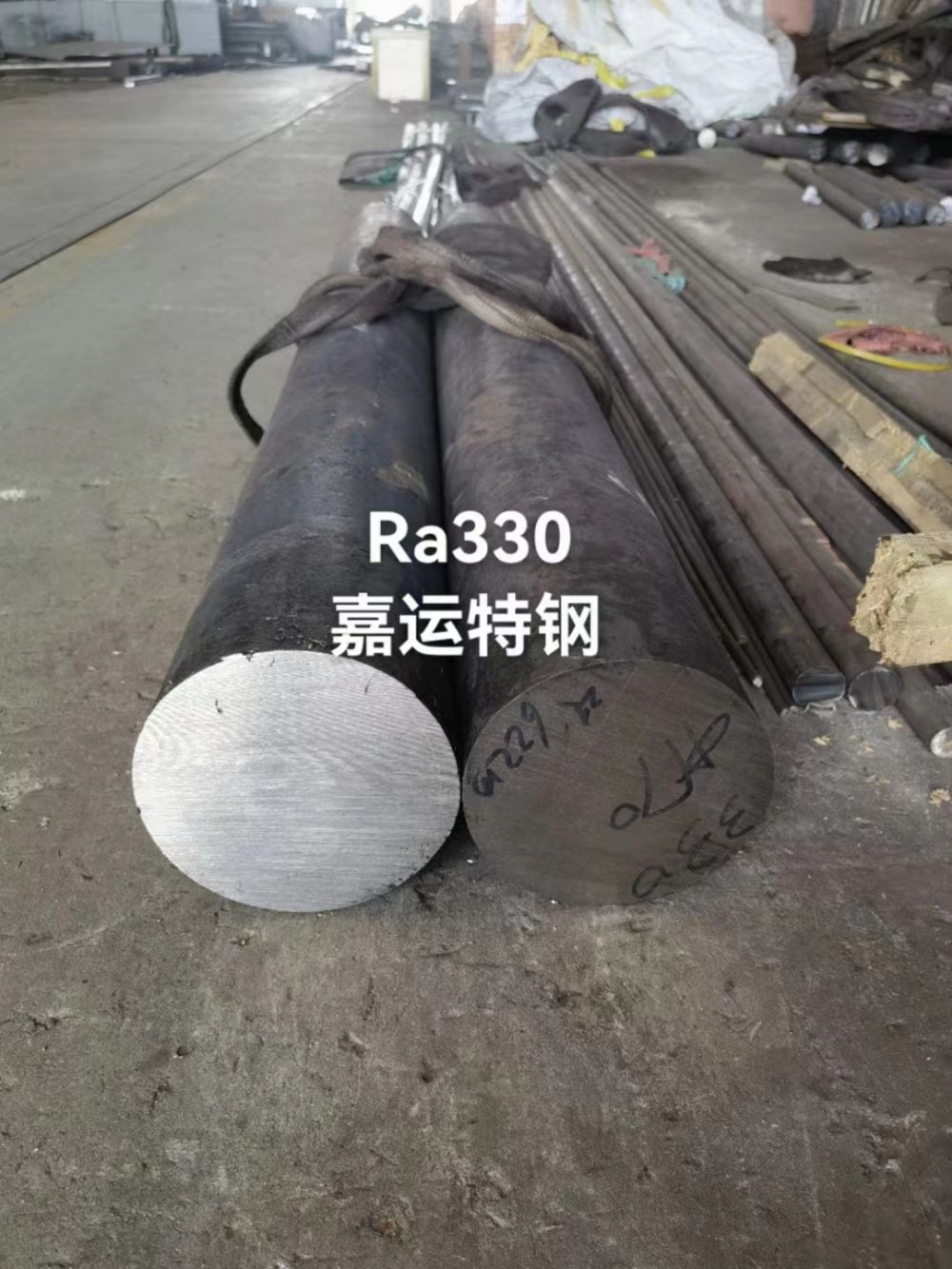
Corrosion resistance: when the mechanical properties and corrosion resistance of martensitic steels are insufficient, the 17-4 PH is suitable for use in marine environments. It has a combination of very good mechanical properties and corrosion resistance.
In standing seawater, 17-4 PH is susceptible to crevice corrosion. This requires additional protection.
Machining: 17-4 PH can be machined in the hardened and solution-annealed condition. Depending on the hardness, the machinability varies, this will depend on the condition.
Heat treatment
Between 1020°C and 1050°C the material 17-4 PH is solution-annealed. This is followed by a rapid cooling - water, oil or air. This depends on the cross-section of the material.
To ensure complete conversion from an austenite to a martensite, the material must have the ability to cool down in room temperature.
Processing
Polishing |
is possible |
Cold forming |
is not possible |
Shape processing |
is possible, depending on the hardness |
Cold diving |
is not possible |
Free-form and drop forging |
is possible |
Physical Properties
Density in kg/dm3 | 7,8 |
Electrical resistance at 20°C in (Ω mm2)/m | 0,71 |
Magnetisability | available |
Thermal conductivity at 20°C in W/(m K) | 16 |
Specific heat capacity at 20°C in J/(kg K) | 500 |
Calculate the weight of the required material quickly »
Chemical composition
17-4PH |
C |
Si |
Mn |
P |
S |
Cr |
Mo |
Ni |
V |
min. |
bis |
bis |
bis |
bis |
bis |
15 |
bis |
3 |
|
max. |
0,07 |
0,7 |
1,0 |
0,04 |
0,03 |
17,5 |
0,6 |
5 |
|
17-4PH |
Al |
Cu |
N |
Nb |
Ti |
Sonstiges |
min. |
|
3,0 |
|
5xC |
|
|
max. |
|
5,0 |
|
0,45 |
|
|
Advantages of saw cut
The processing with the saw is a mechanical processing of the material, which results in a significantly lower unintended deformation and increased hardness for the existing structure, such as the thermal cutting.
Thus, the machined workpiece has a homogeneous structure even at the edge, which does not change in the continuation of the material.
This circumstance allows immediate finishing of the workpiece with milling or drilling . So it is not necessary to anneal the material or make a similar operation beforehand.

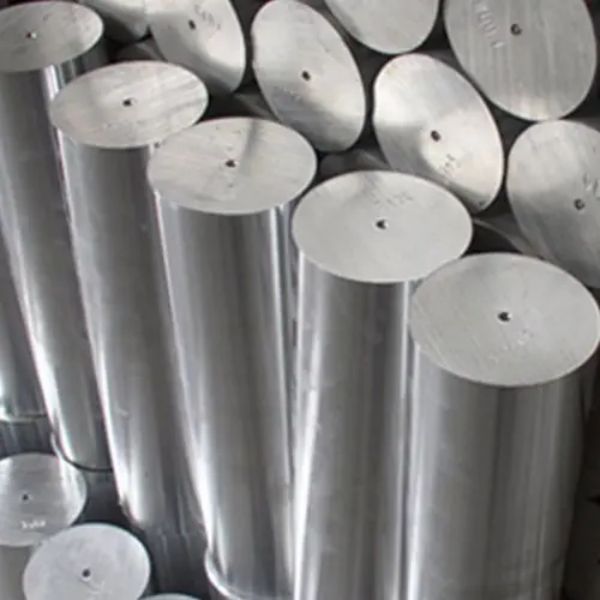
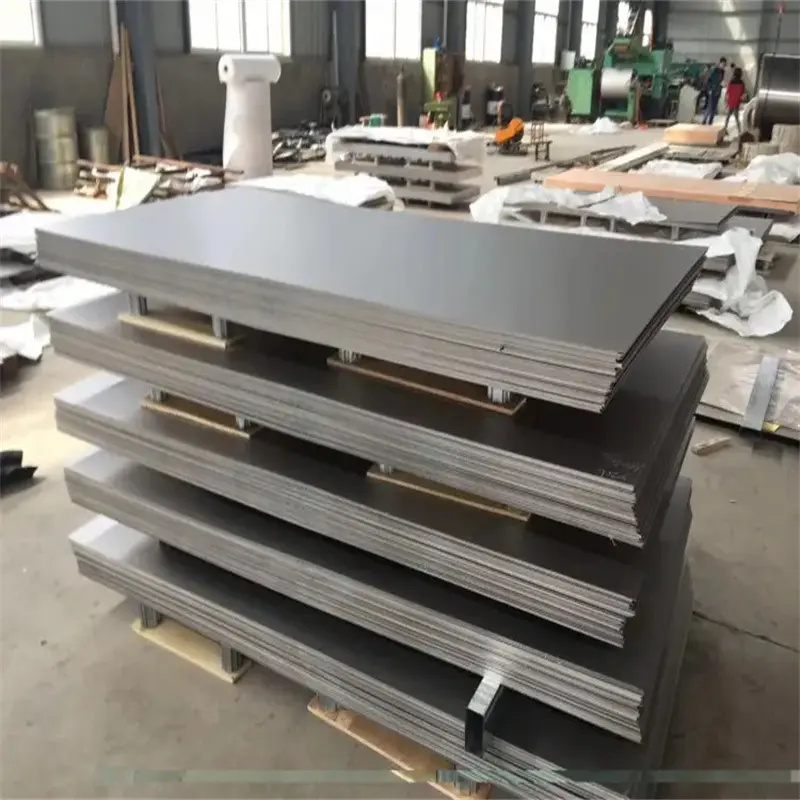
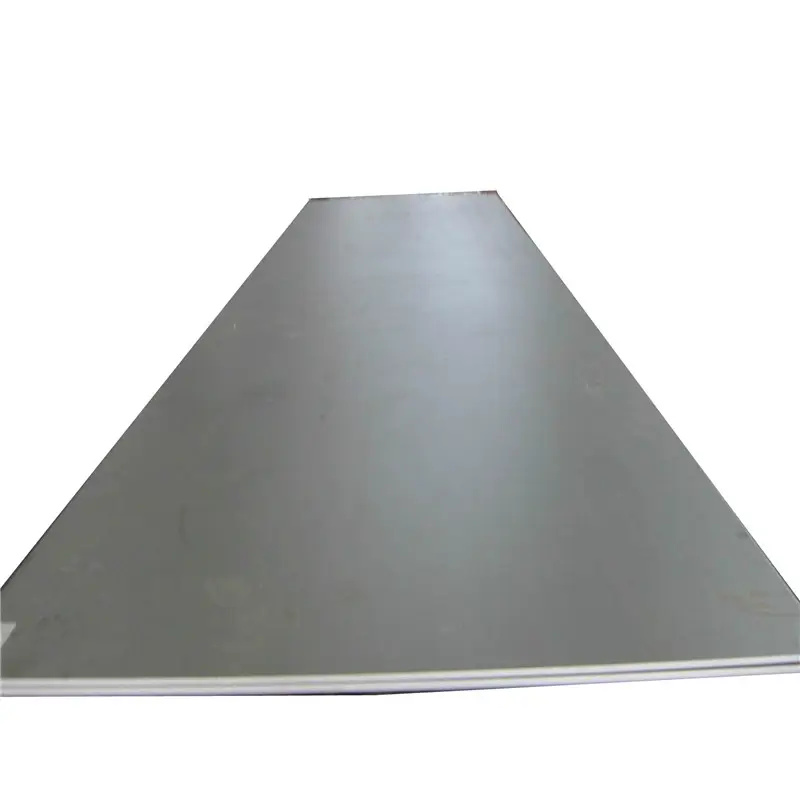