1: Heating For Hastelloy B-2 alloys, it is very important to keep the surface clean and free from contaminants before and during heating. Hastelloy B-2 becomes brittle if heated in an environment containing sulfur, phosphorus, lead, or other low-melting metal contaminants, mainly from marker marks, temperature indicating paint, grease and liquids, smoke. The flue gas must contain low sulfur; for example, the sulfur content of natural gas and liquefied petroleum gas does not exceed 0.1%, the sulfur content of urban air does not exceed 0.25g/m3, and the sulfur content of fuel oil does not exceed 0.5%. The gas environment requirement for the heating furnace is a neutral environment or a light reducing environment, and cannot fluctuate between oxidizing and reducing. The flame in the furnace cannot directly impact Hastelloy B-2 alloy. At the same time, the material should be heated to the required temperature at the fastest heating speed, that is, the temperature of the heating furnace should be raised to the required temperature first, and then the material should be put into the furnace for heating.
2: Hot working Hastelloy B-2 alloy can be hot worked in the range of 900~1160℃, and should be quenched with water after processing. In order to ensure the best corrosion resistance, it should be annealed after hot working.
3: Cold working Hastelloy B-2 alloy must undergo solution treatment. Since it has a much higher work hardening rate than austenitic stainless steel, the forming equipment should be carefully considered. If a cold forming process is performed, interstage annealing is necessary. When the cold working deformation exceeds 15%, solution treatment is required before use.
4: Heat treatment The solution heat treatment temperature should be controlled between 1060~1080°C, and then water-cooled and quenched or when the material thickness is above 1.5mm, it can be quickly air-cooled to obtain the best corrosion resistance. During any heating operation, precautions must be taken to clean the surface of the material. Heat treatment of Hastelloy materials or equipment parts should pay attention to the following issues: In order to prevent heat treatment deformation of equipment parts, stainless steel reinforcement rings should be used; the furnace temperature, heating and cooling time should be strictly controlled; Carry out pretreatment to prevent thermal cracks; after heat treatment, 100% PT is applied to the heat-treated parts; if thermal cracks occur during heat treatment, those who need to repair welding after grinding and eliminating should adopt a special repair welding process.
5: Descaling The oxides on the surface of the Hastelloy B-2 alloy and the stains near the welding seam should be polished with a fine grinding wheel. Since Hastelloy B-2 alloy is sensitive to oxidizing medium, more nitrogen-containing gas will be produced during the pickling process.
6: Machining Hastelloy B-2 alloy should be machined in an annealed state, and it must have a clear understanding of its work hardening. The hardened layer should adopt a larger feed rate and keep the tool in a continuous working state.
7: Welding Hastelloy B-2 alloy weld metal and heat-affected zone are easy to precipitate β phase and lead to poor Mo, which is prone to intergranular corrosion. Therefore, the welding process of Hastelloy B-2 alloy should be carefully formulated and strictly controlled . The general welding process is as follows: the welding material is ERNi-Mo7; the welding method is GTAW; the temperature between the control layers is not more than 120°C; the diameter of the welding wire is φ2.4 and φ3.2; the welding current is 90~150A. At the same time, before welding, the welding wire, the groove of the welded part and the adjacent parts should be decontaminated and degreased. The thermal conductivity of Hastelloy B-2 alloy is much smaller than that of steel. If a single V-shaped groove is used, the groove angle should be around 70°, and a lower heat input should be used. Post-weld heat treatment can eliminate residual stress and improve stress corrosion cracking resistance.
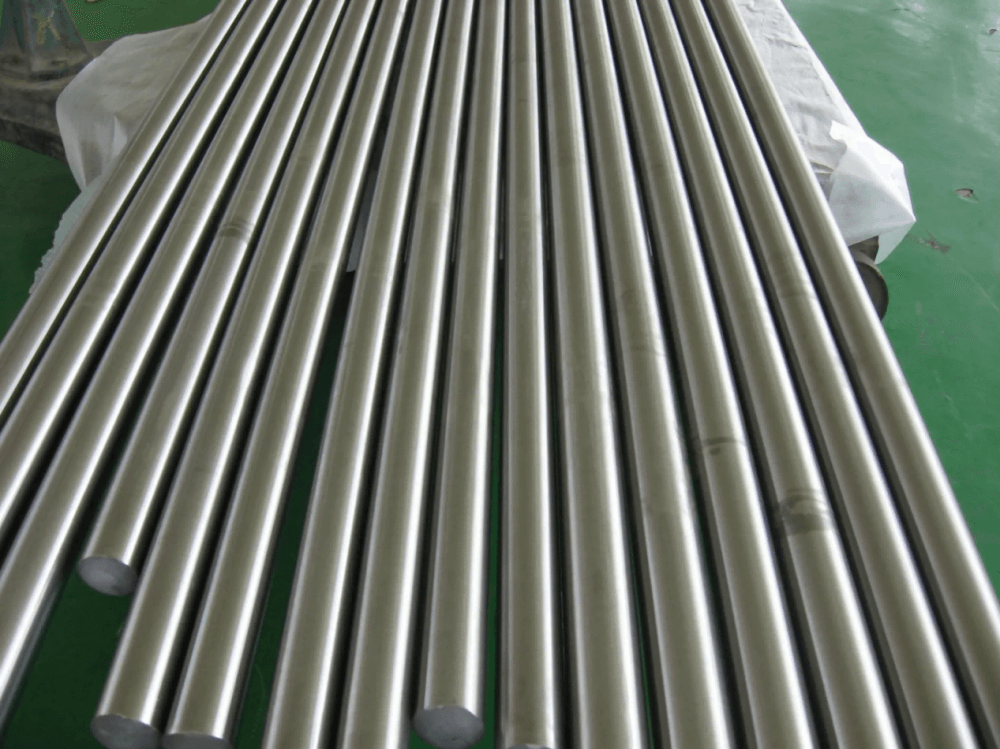
Post time: May-15-2023